Compliance Maintenance &Testing
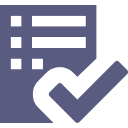
What is compliance testing?
Compliance testing is about ensuring that your business is compliant with all of the laws that surround commercial buildings and premises. This largely involves keeping your employees safe through compliance maintenance.
Why do we need compliance testing?
Compliance testing is an essential part of your building maintenance requirements. It ensures that the building is safe and legally compliant. It is your responsibility to keep your team safe. You wouldn't let them drive a company car without insurance, so it is key to keep your building compliant too.
What is involved in compliance testing?
It is a series of tests. Typical tests include:
Emergency light testing - Flick test and Dead test.
Fire Risk Assessments - Ensuring your team remain safe in the event of a fire
Water Treatment: Hygiene - testing for Legionella. Temperature - ensuring hot water does not scald your employees.
Fire Extinguishers - Checking the expiry dates and testing.
PAT testing: Ensuring electrical equipment is tested annually.
5 year fixed wiring inspection - Ensuring the electrical wiring has not been compromised.
Why should I get C|S|M in to complete my compliance testing?
C|S|M have worked for many years with many clients ensuring that their premises remain compliant. Many of our clients book us in for an annual visit to ensure most of these tests are completed in one day. C|S|M are dedicated to maintenance in London and the major cities of the UK. We work in commercial maintenance and pre planned maintenance and have both the knowledge and experience to make your buildings safe and compliant.
What would happen if we were found not to be compliant?
The main way in which you would be discovered to be none compliant would be if there was an accident with one of your employees on your site. A serious accident has to be reported to the HSE, which ultimately results in an investigation, should you be found not to be compliant in any of the regulations in reference to protecting employees, you may be prosecuted and fined.
The table below demonstrates which laws are applicable for compliance in commercial premises. Not all partsof maintenance are related to a law, but it is important to consider some of these elements in regular maintenance as the table suggests.
To download a copy of this table please click here.
Aspect |
Requirements |
Frequency |
Applicable Law |
Boilers (gas) |
Regular servicing, ‘Gas Safe’ Inspection Provision of Gas Safety Certificate |
Annually |
Gas Safe |
Electrical System |
Fixed electrical installation inspection and testing |
5 yearly or 20% per year |
NECEIC Regulations Electricity at Work Regulations 1989 |
Emergency Lighting |
Testing Replacement of bulbs and batteries |
Monthly flick test, Six monthly 1 hour test, Yearly discharge test – 3 hours |
Regulatory Reform (Fire Safety) Order 2005 |
Fire Alarm |
Regular maintenance, Testing of call points and sounders, Testing of detectors |
Weekly alarm test Yearly test of detectors |
Regulatory Reform (Fire Safety) Order 2005 |
Fire Extinguisher |
Servicing and inspection |
Annual |
Regulatory Reform (Fire Safety) Order 2005 |
Fire Doors |
Maintenance and inspection |
Annual |
Regulatory Reform (Fire Safety) Order 2005 |
Lighting Protection |
Inspection |
Annual |
Electricity at Work Regulations 1989 |
Lifts |
Servicing, Insurance Inspection |
6 months |
Lifting Operations and Lifting Equipment Regulations 1998 |
PAT Testing |
Visual inspection, Formal PAT test |
Annual – three yearly depending on risk |
Electricity at Work Regulations 1989 |
Pressure Systems |
Maintenance and inspection |
Generally annually |
Pressure Systems Safety Regulations 2000 |
Emergency Communication System |
Testing |
Monthly |
Regulatory Reform (Fire Safety) Order 2005 |
Water Hygiene |
Disinfection, Flushing, Microbiological Testing Review |
Weekly flushing low use outlets Monthly temperature checks Quarterly microbiological sampling Disinfection when required |
Control of Substances Hazardous to Health Regulations 2002
L8 ACOP |
Expansion Vessels |
Maintenance/Testing |
As per L8 recommendations |
COSHH 2002 / L8 |
Cold Water Storage |
Cleaning / Temperature Checks |
Generally Annual cleaning / inspection, monthly temperature checks. |
COSHH 2002 / L8 |
Fall Arrest |
Testing and Inspection |
At least every 12 months |
Working at Height Regulations 2005 BSEN795: ‘Protection Against Falls From Height, Anchorage Devices, Requirements And Testing’ |
Fire Risk Assessment |
Inspection / Review |
Generally annually |
Regulatory Reform (Fire Safety) Order 2005 |