Pre-Planned Maintenance
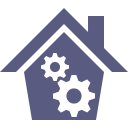
What is Pre-planned maintenance?
Pre-planned maintenance can also be referred to as Pre-Planned Preventative Maintenance (PPM), Scheduled maintenance or simply planned maintenance. It is the process of ensuring that you have service agreements in place for any of your assets in your business. Asset registers are often used to ensure that this planned maintenance is completed at the right intervals. It also refers to preventing possible future issues, such as blocked drains and air conditioning issues by cleaning and servicing them to keep them well maintained resulting in fewer reactive maintenance issues occurring.
It's a bit similar to taking a flu jab. If you take a flu jab you wont catch flu, but if you don't have a flu jab you are taking the risk that something may go wrong and you may end up with flu and then you will have to face the consequences of being ill and having to take reactive medicine. It's the same in maintenance, preventative maintenance can stop things going wrong, and if you don't do it, you may be lucky and things may not go wrong, but that is a risky strategy, because if something does go wrong, then reactive maintenance is required which is often more costly.
Why do I need Pre planned maintenance?
Pre planned maintenance is necessary in any retail, restaurant, healthcare, dental, office and educational building to ensure the continuation of business without interruption. Pre planned maintenance can be completed at your convenience, rather than as an emergency or re active maintenance that must be fixed as a priority, where the issue itself determines the timings and cost.
What does pre planned maintenance involve?
Pre planned maintenance often involves pre determining a set list of issues that need to be completed, for example, air conditioning services, drainage clearance, pipe cleans, boilers serviced, cookers, dishwashers, heaters, re-lamping, clearing gutters, re painting windows, doors, checking door mechanisms and locks. This list would be agreed with each individual client as each property maintenance requirements are different. The C|S|M team then turn up at your convenience or at a regular time or annually to complete this planned maintenance.
Will it disrupt my business?
No, C|S|M will operate at a time that is convenient to you. We can work around your busy times or work out of hours if it works better for your business.
What are the advantages of pre planned maintenance?
The advantages of pre planned maintenance are that it ultimately saves a company time and money, let alone the hassle factor of emergency and re active maintenance.
Why should I employ C|S|M to complete my pre planned maintenance?
C|S|M have both the experience and knowledge to be able to assist you with your pre planned maintenance. We can not only assist in creating a list that will assist your business to manage it's assets and keep re-active maintenance to a minimum, but we can also complete the works as if we were the elves in night, leaving you to get on with what you do best.
One of the main advantages of pre-planned maintenance is that it ensures many laws and regulations are met in terms of building compliance. Below is a table of works that can be completed as part of on going pre-planned maintenance and the law or regulation that is related to.
To download a copy of this table please click here.
Aspect |
Requirements |
Frequency |
Applicable Law |
AHU’s |
Filter changes Regular maintenance |
|
|
BMS |
Regular maintenance |
|
|
Boilers (gas) |
Regular servicing, ‘Gas Safe’ Inspection Provision of Gas Safety Certificate |
Annually |
Gas Safe |
CCTV |
Cleaning of exterior lenses |
|
|
Drainage |
Rodding of drains |
|
|
Electrical System |
Fixed electrical installation inspection and testing |
5 yearly or 20% per year |
NECEIC Regulations Electricity at Work Regulations 1989 |
Emergency Lighting |
Testing Replacement of bulbs and batteries |
Monthly flick test, Six monthly 1 hour test, Yearly discharge test – 3 hours |
Regulatory Reform (Fire Safety) Order 2005 |
Fan Coils HVAC |
Regular servicing |
|
|
Fire Alarm |
Regular maintenance, Testing of call points and sounders, Testing of detectors |
Weekly alarm test Yearly test of detectors |
Regulatory Reform (Fire Safety) Order 2005 |
Fire Extinguisher |
Servicing and inspection |
Annual |
Regulatory Reform (Fire Safety) Order 2005 |
Fire Doors |
Maintenance and inspection |
Annual |
Regulatory Reform (Fire Safety) Order 2005 |
General Lighting |
Replacement |
|
|
Guttering |
Cleaning |
|
|
Lighting Protection |
Inspection |
Annual |
Electricity at Work Regulations 1989 |
Lifts |
Servicing, Insurance Inspection |
6 months |
Lifting Operations and Lifting Equipment Regulations 1998 |
PAT Testing |
Visual inspection, Formal PAT test |
Annual – three yearly depending on risk |
Electricity at Work Regulations 1989 |
Pest Control |
Changing of bait |
|
|
Pressure Systems |
Maintenance and inspection |
Generally annually |
Pressure Systems Safety Regulations 2000 |
Revolving/Automatic Doors |
Maintenance and inspection |
|
|
Emergency Communication System |
Testing |
Monthly |
Regulatory Reform (Fire Safety) Order 2005 |
Toilet Extract |
Cleaning |
|
|
Water Cooler Machine |
Maintenance |
|
|
Water Hygiene |
Disinfection, Flushing, Microbiological Testing Review |
Weekly flushing low use outlets Monthly temperature checks Quarterly microbiological sampling Disinfection when required |
Control of Substances Hazardous to Health Regulations 2002
L8 ACOP |
Water Softener |
Maintenance |
|
|
Windows |
Cleaning |
|
|
Expansion Vessels |
Maintenance/Testing |
As per L8 recommendations |
COSHH 2002 / L8 |
Cold Water Storage |
Cleaning / Temperature Checks |
Generally Annual cleaning / inspection, monthly temperature checks. |
COSHH 2002 / L8 |
Pumps |
Maintenance |
|
|
Radiators |
Maintenance |
|
|
Fall Arrest |
Testing and Inspection |
At least every 12 months |
Working at Height Regulations 2005 BSEN795: ‘Protection Against Falls From Height, Anchorage Devices, Requirements And Testing’ |
Trace heating |
Testing and Inspection |
|
|
UPS |
Testing and Inspection |
Generally 6/12 monthly |
|
Fire Risk Assessment |
Inspection / Review |
Generally annually |
Regulatory Reform (Fire Safety) Order 2005 |
Where does C|S|M work?
C|S|M work all over the UK, in all of the major cities. The majority of our work tends to be focused in London, and as a result of this we have many handymen and maintenance professionals readily available to assist you.